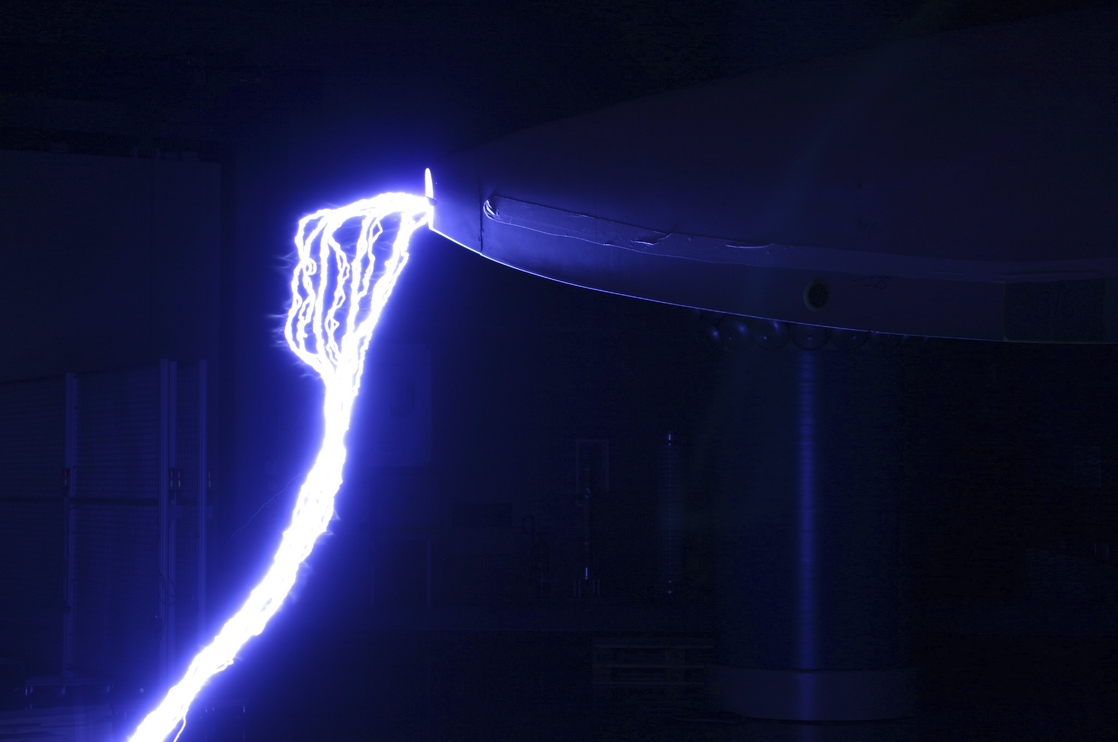
Innovating at lightning speed: How a team of LM Wind Power engineers developed the industry’s first lightning protection system
At any given moment during the day, 2,000 thunderstorms are active around the world. That amounts to sixteen million of such severe weather events per year. With wind turbines stretching up to a couple hundred meters above ground, very often in flat areas with no other big structures nearby, they are easy targets for lightnings. Some estimate that every blade will be struck, on average, 128 times over a period of 20 years, potentially causing important economic damage.
Although wind turbine blades are highly susceptible to lightning strikes, this can be dealt with through lightning protection systems. In fact, today it is unthinkable not to equip wind turbines with such systems, but that wasn’t always the case: “Back in the 80s and early 90s, there was a belief that glass fiber was non-conductive, isolated, and therefore blades could not be struck by lightnings,” recalls Lars Bo Hansen, Advanced Lead Engineer, Electro-System. “Wind turbines were relatively small, with rotor diameters in the range of 20-25m. Even when they were struck by a lightning, they could be easily repaired, often replacing the tip of the blade, which was a separate piece in blades with tip brake system,” adds Jesper Mansson, Chief Technical Advisor & former leader of the LPS team.
However, as blades grew in length and wind turbines grew in size, they became more susceptible to lightning strikes. Back then, the still young wind industry had a challenge that it needed to address on its way to demonstrate that it was a real solution to competitively decarbonize the energy system.
If there is a problem, there is also a solution
If the wind power history teaches us something, it’s that wherever there is a problem, engineers manage to also find a solution. And it was a team of LM Wind Power experts the first ones in the industry to tackle this issue, living up to the company’s reputation as a pioneer and technology leader.
“The first LPS consisted of a receptor on the tip for the lightning to strike there and then go down through a lightning current down-conductor for evacuation. In this way you could control where it hit, and evacuate the current in a controlled way, avoiding damage to the blade,” explains John Korsgaard, Senior Director, Engineering Excellence & former leader of the LPS team. “In these first systems, there was just one receptor in the blade tip, and we hoped the lightning would strike there, but in reality, we saw that it could strike in different places, and therefore a multi-receptor system was developed,” adds Yaru Méndez, Director, Electro Systems.
Back then there were no previous experience with LPS for wind turbines, nor test facilities to validate new technologies. The team developed these systems based on available knowledge from other industries, plus some recommendations from a group of Danish utilities, US experts, IEC standardization work and research institutes based on operation and research experience.
LM Wind Power has a solid track record of innovation and record-breaking blades. Technology evolution can sometimes bring new challenges, exactly what happened to the LPS with the turn of the century: “At LM Wind Power we were some of the first to introduce carbon blades as a way of improving their performance and weight, but carbon is also an extremely conductive material. We saw that the carbon fiber was struck by lightning as often as the actual receptors and came up with a diverter strip to evacuate the current in a controlled manner,” explains Lars Bo Hansen, one of the inventors of such a solution.
Innovation from there has been incremental, but the strong foundations were laid by this team of LM Wind Power engineers. They, once again, positioned the company at the forefront of the wind power evolution until becoming what it is today: an affordable, safe, reliable and sustainable source of electricity that holds the answer to a net zero future.