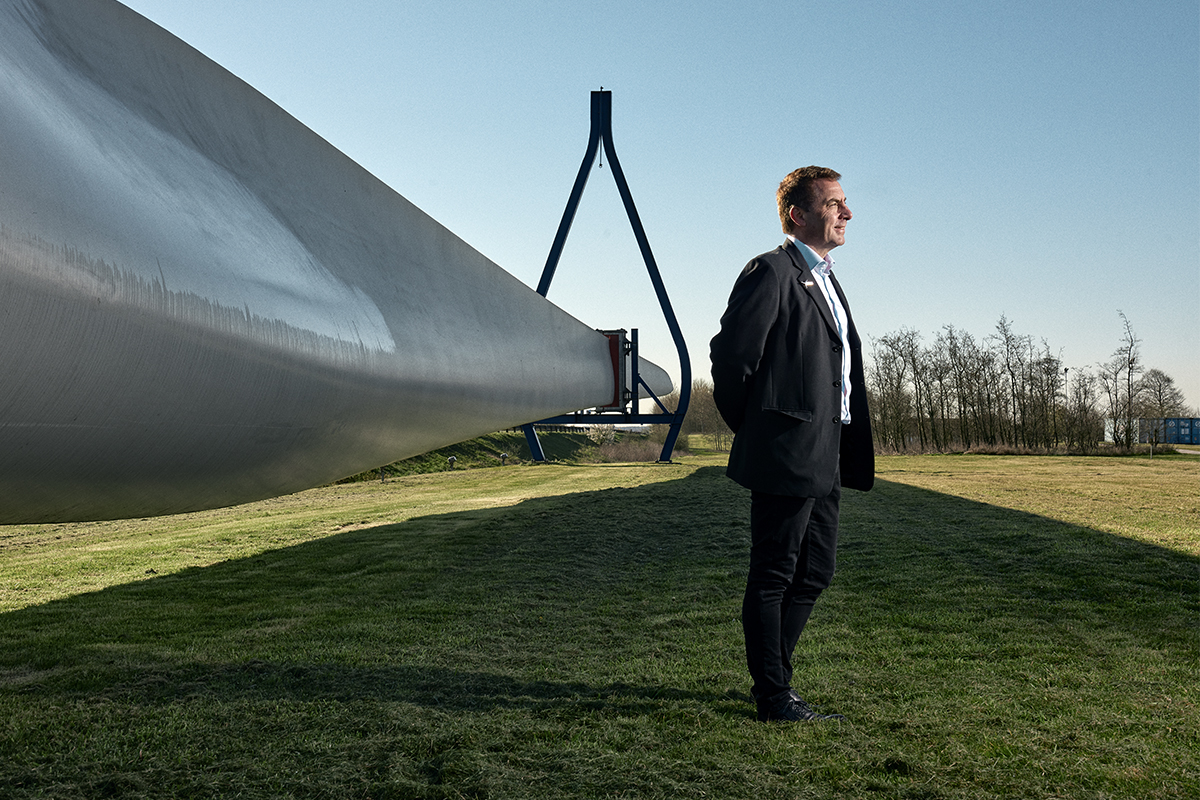
The next step: Re-thinking resource use to reach a fully sustainable wind power industry
As a wind industry veteran, John Korsgaard, Sr. Director Engineering Excellence and Chair of the DecomBlades Steering Committee deliberates on the need to look beyond operational control as we continue to explore avenues to reduce our carbon footprint and accelerate the transition to a circular economy.
In my career spanning over three decades at LM Wind Power I have been closely involved in designing wind turbine blades of varying lengths – as small as 12 meters up to our largest blade today at 107 meters in length. During that journey, I have also witnessed LM Wind Power launch a sustainability strategy and reach a key milestone when we became the first company in the wind industry to achieve carbon neutral operations in 2018.
To go carbon neutral, we followed ‘10 Steps’, which included accounting for our emissions, reducing them as much as possible, switching to 100% renewable electricity to power our sites and balancing our remaining footprint with offsets. In following these steps, we also uncovered significant cost savings from energy efficiency and waste reduction – $2.6 million in savings from energy efficiency in the first year of the carbon neutral program alone – proving that sustainability ambitions and business priorities can go hand-in-hand.
As we continue to find ways to reduce our carbon footprint, it’s time to take the next step. We need to re-think the ways we manage resources throughout the full blade life cycle.
LOOKING BEYOND OUR OPERATIONAL CONTROL
Presently, the wind power industry is witnessing one of the busiest periods in history with the demand for clean energy surging. Newly announced onshore and offshore projects are indicative of how this clean energy alternative is cementing its position as a significant addition to the world’s energy mix. But, as demand for our products grows (and so does the size of our blades), we will also consume more resources to produce the blades. The next stage of our sustainability journey is about managing these valuable resources, optimizing their value throughout the lifetime of a blade and giving them a new life within a circular economy.
Nearly 90% of the carbon footprint in a blade’s life cycle is generated upstream: 76% during resource extraction and 13% during manufacturing. To put that in perspective, a blade’s end-of-life – if it is sent to a landfill - represents around 1% of the emissions from its lifetime.
As a blade manufacturer, our position in the value chain best enables us to influence the emissions that occur upstream, before the blade is installed on a wind turbine. We need to work with our supply chain to reduce CO2 emissions from resource extraction, including reducing waste in manufacture of materials used in making blades. We also need to collaborate with our supply chain to use more recycled materials into blade materials, to minimize the use of virgin materials.
We also can significantly impact resource use by reducing the waste in our own production, where around 25% of materials currently go to waste, and only around 25% of that waste is recycled. Reducing the amount of production waste isn’t easy, as it requires establishing new value chains for cost-effective and environmentally sustainable ways to handle our waste streams. In the ZEBRA (Zero wastE Blade ReseArch) project, LM Wind Power will design and manufacture fully sustainable wind turbine blades, working with a consortium that represents the full value chain from development of materials, to blade manufacturing, wind turbine operation, and eventually recycling of the decommissioned blade material.
Developing viable value chains for recycling blade production is closely tied to our efforts to address another resource management challenge for the wind power industry: sustainable solutions for handling blades when they reach their end-of-life. Already today around 85%-90% of a wind turbine’s mass today is recycled. However, the blades are more challenging to recycle, largely due to their thermoset composite materials which are difficult to separate.
In our pursuit of sustainable ways to manage resources across the blade life cycle, sending end-of-use blades to landfill clearly represents a waste of resources. There are already technologies that can recycle wind turbine blades – the most mature are mechanical grinding, cement co-processing and pyrolysis. The challenge is scaling up these technologies to handle the coming volumes of end-of-life blade waste, as well as waste from blade manufacturing and the waste from other composite manufacturing sectors. Our efforts to address this recycling challenge have led to the start of the DecomBlades project in Denmark in January. This consortium brings together the wind industry, the recycling industries and universities to form the basis to commercialize viable recycling solutions.
TAKING STEPS TOGETHER
We still have a winding road ahead on the journey to become a fully sustainable wind power industry. The ‘10 Steps’ LM Wind Power followed to become a carbon neutral business were about looking at our own operations, demonstrating the value of sustainability toward our business objectives as we become leaner and greener. That mission continues. We are taking the next step to become a truly sustainable, circular product. We won’t make it very far if we take that step alone. It’s encouraging (and essential) to see leading companies in the wind industry and beyond discussing how we can partner up and take this step together to accelerate the transition to a circular economy.